Chemical industry
In the manufacture of products and intermediates in the chemical, petrochemical and flavours and fragrance sectors, large volumes of precious metal catalysts are used. These often form waste streams which are both difficult and valuable.
Tailor made service
Mastermelt has the knowledge and experience to provide tailored reclamation and recycling services that optimises precious metal recoveries from waste, returning significant value and supporting customers with their environmental and social governance (ESG) commitments. Our services are suitable for the treatment of small scale (R&D and pilot) through to multi-tonnage production campaigns.
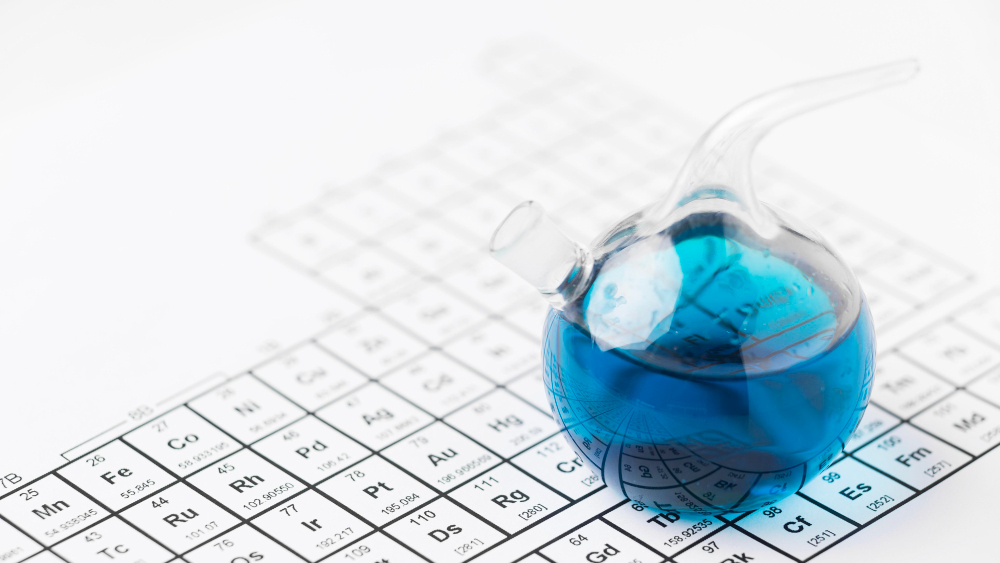

Sustainable metal recycling for the chemical industry
Mastermelt partner with various companies in many chemical sectors to provide a sustainable recycling and metal loop reclamation service that optimises metal recovery, enables the reuse of valuable metals, and improves cash flow.
How can metal be recovered from chemical waste streams?
Controlled thermal pre-treatment is the most effective way to recover precious metals from heterogeneous catalyst waste. The use of homogeneous catalysts in some industries, such as flavours and fragrances, has led Mastermelt to develop innovative solutions including distillation and metal scavenger recovery systems to capture precious metals.
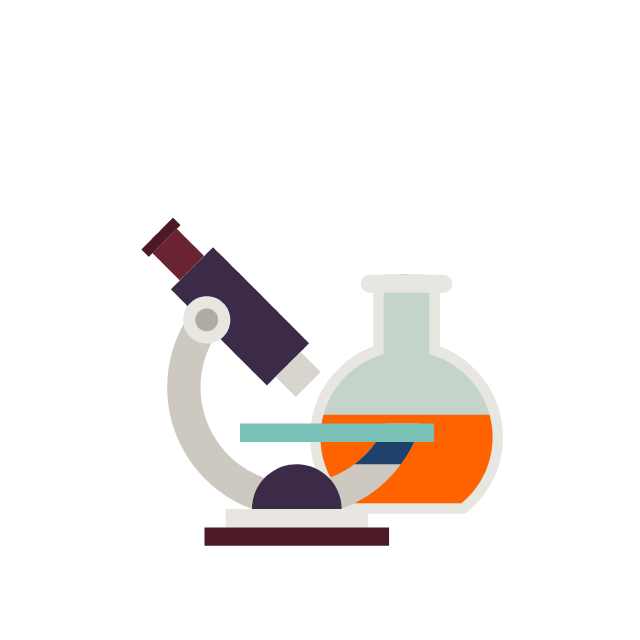
What materials from the chemical industry can be recycled?
Palladium and Rhodium are key precious metals used in the chemical industry, which are found in numerous waste streams from chemical processing:
Click on the tabs to view
PGM’s on Carbon, Alumina, Silica, Celite
PGM Organometallic solutions
PGM’s from reactor sumps/drains
PGM’s on Carbon, Alumina, Silica, Celite
Purification Media
PGM’s on Carbon on silica
Purification; cloths, cartridges
Aqueous electroplating PGM solutions
Contaminated gloves, overalls, wipes
What is the process for reclaiming metal from chemical industries?
No two waste streams are alike; we evaluate each material type on a case-by-case basis to establish the most effective processing route to maximise precious metal recoveries. We have a particular interest in recycling metal from difficult materials and utilise the capabilities of our state-of the-art instrumentation and specialists in precious metal chemistry and recovery.
Understanding
Understanding your process is important, as this will help determine the treatment route and matrix effects, such as any residual solvents and any base metals present.
Pre-treatment
How you pre-treat waste streams such as steam treatments, washing to remove solvents and nitrogen purging will also help to define the treatment method required, as well as the type of filtration system/media or other methods you use to collect and isolate spent catalyst waste streams.
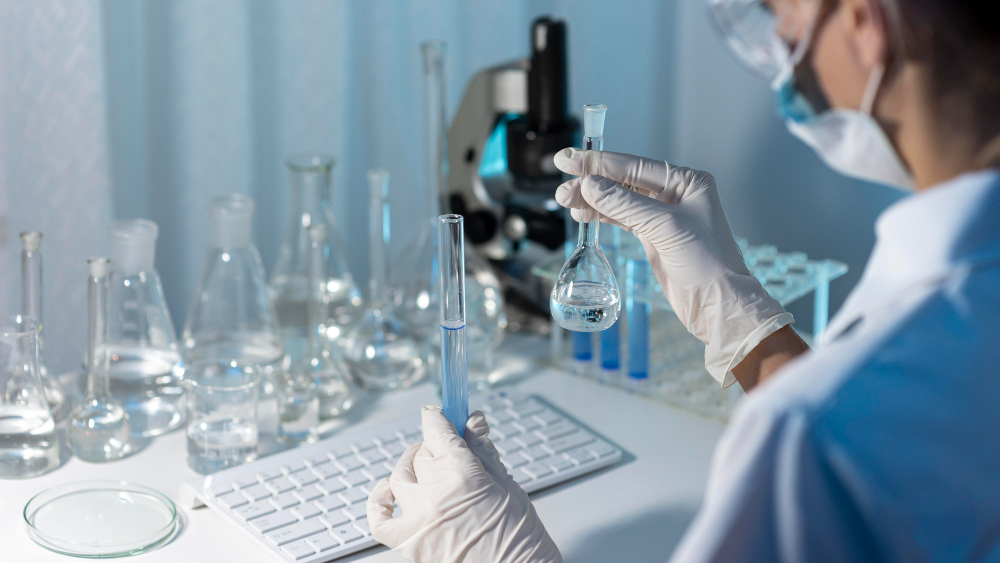
The process for reclaiming metals from chemical manufacturing comprises:
Once we understand your process, we will conduct analysis on a small sample of waste to perform matrix evaluation and thermogravimetric properties of the material.
Technical scale-up of the tailored process route, which is monitored using rigorous process controls, ensures safe and effective production scale validation.
We will inspect the first delivery of material to ensure that it conforms with the sample previously provided. We will record details including photographing the material, before processing starts.
Initial processing of a small sample – normally 10-25kg. It’s then monitored by our technicians and process measurements compared against the process design.
These benchmarks could include the exotherm rate, ash %, O2 depletion rate, tracer spike analysis.
Assuming the initial trial benchmarks are within limits, then the volumes will be increased to a minimum production scale.
OPTIMISATION
Efficient and expedient processing of large volumes of the waste stream, underpinned by performance benchmarking, resulting in industry leading precious metal returns.
PRODUCTION
When the performance benchmarks have been met, our production technicians look to optimise the throughput of the material, using Mastermelt’s unique processing equipment and operating methods to increase the throughput.
RECOVERY
Knowing the benchmark envelope will enable the maximum amount of precious metal recovery companies. This will be measured by our class leading sampling and analysis techniques.
SETTLEMENT
A full report is generated and sent to the customer to gain agreement. Metal can be transferred to your catalyst suppliers account to be used to manufacture fresh catalyst or priced on the London metal market as per your instruction.
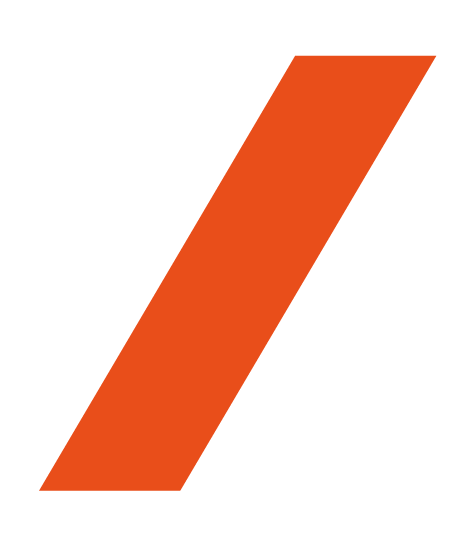
Resources
GET IN TOUCH
To arrange a process audit with one of our Technical Sales Managers Contact us.